Brake rotor installation guide.
- Jerry DeMarino
- May 11, 2021
- 5 min read
Updated: Jun 30, 2021
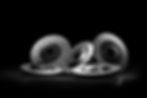
A question commonly asked by customers is how to correctly install brake disc rotors and any bedding in procedure which might need to followed.
Removal.
“We always recommend that you ask a qualified mechanic to carry out installation of new brake disc rotors if you have no prior mechanical experience.”
Installing new brake disc rotors is a common occurrence. Depending on driving style and mileage its not uncommon to have to change your brake pads every 18-24 months, with rotor on average being changed once every two years. We must stress however, every vehicle, driver and driving style is different and as such you should regularly check the condition of your brake pads and rotors according to your driving style and annual mileage.
Before installation begins, the existing brake pads and rotors must first be removed. The following steps are intended only as a guide:
1) Where possible have your vehicle raised off the ground by means of a workshop ramp (two or four post). If you do not have access to a workshop or ramp then it is important to find a flat hard standing surface where the vehicle can be raised by means of a manual jack. It is important prior to raising the vehicle that the jacking points are identified and jacking pads aligned before lifting commences, in addition wheels nuts (or bolts) should be slightly loosened. It is imperative not to wind the wheel bolts out excessively or fully until the wheel being lifted is firmly off the ground.
2) Before the brake rotors can be removed the brake caliper first has to be released from the cast upright. The 'upright' is the cast steel (or aluminium) body which in the case of the front of the car connects your suspension strut, steering rack, suspension arms and wheel hub together. There are many alternate types of brake caliper, many of which utilise alternative bolt sizes to retain them. Typically there will be two bolts holding the caliper body to the upright which when released enable the caliper body to slide away from the centre of the disc. Prior to releasing the caliper retaining bolts, it is worth having a number of heavy duty zip ties to hand (as once the caliper is released the full weight would be pulling on the brake line if you do not offer the body with support). Most mechanics prefer to zip tie the caliper body to the coil spring on the suspension, placing a cloth between the body of the caliper and the body of the strut (to prevent marking the caliper body). By doing this the caliper is supported without exerting pressure on the fragile brake line and in addition the caliper body is nicely out of the working area.
3) Removal of the existing brake disc rotor:. In almost all cases there will be at least one (if not two) small retaining bolts which secure the rotor to the bearing hub face. The small retaining bolts are typically found with a Torx face (size T30), or alternatively a 6mm Allen Key. Due to the length of time these bolts have been in place (and the excessive temperature cycles they are subject to), it is often worth first coating them with maintenance spray and leaving them to soak for five minutes prior to removal. Once removed the brake disc rotor can be lifted away from the wheel bearing hub face. If you find the disc is stubborn to remove (often because of light corrosions between the mating faces) then a light tap with a rubber mallet hammer is acceptable.
4) Removal of the brake pads: The final part of the procedure is to remove the old brake pads. It is often down to personal preference, however it is typically deemed that for every second change of brake pads, your rotors should also be replaced. Again, this is a guide only (as condition would often dictate change) and it is not uncommon for vehicle owners to replace both the brake pads and brake rotors at the same time, ensuring the best possible performance. To remove the old brake pads; they will often fall away from the body of the brake caliper (during the earlier caliper body removal), however they can also need a helping hand. If you find your old brake pads cannot be pushed out by hand then you can gently lever them (or income cases lift them) away from the body by means of a flat blade screwdriver OR a gentle tap from a small hammer. In both cases be sure to use a soft cloth so as not to mark the caliper body. Excessive force should not be required for this process!
Installation.
So you are ready to fit your new #SHW brake disc rotors. Installation is much the reversal of removal, however there are some additional steps to include.
“Smearing Copper Grease on bolt threads before reinstallation will help prevent corrosion.”
1) Preparation: Before installing your new brake disc rotors and brake pads, first wire brush the outer mating surface of the wheel bearing hub. This will be the face which was visible on removal of the brake disc rotor. Once complete, lightly smear a very thin layer of high temperature copper grease onto the surface. By doing so, this will help prevent corrosion on the outer bearing face and inner brake disc rotor face, allowing easy removal nexuses time around.
2) With the same high temperature grease, lightly smear the threads on the following bolts, again to offer a preventive barrier to corrosion. Be sure the threads are all in good condition and there is no debris or contamination between the thread pitch:
- Caliper body mounting brackets.
- Retaining bolts (brake disc rotor to bearing hub face)
- Wheel bolts (or if the vehicle utilises wheel studs, then apply the same small covering of grease).
3) Ensure your brake pads are supplied with new backing plates. These plates seat behind the brake pad and mate against the inner caliper face. Some brake pad manufacturers often include a small sachet of grease to add to the backing plate, if so follow their instructions for application.
4) Return the brake caliper pistons back to their seated position. To do this follow the below steps:
- Remove the cap from the brake fluid reservoir (usually located under the bonnet and prominent with a yellow cap).
- Investigate if you brake caliper requires you to 'wind' the pistons back into position OR if they are simply pressed back into position. A good indicator as to which type you have is by looking at the surface of the piston face. Pistons which have to be wound back usually have a recessed feature so you can locate and turn the piston. Most new vehicles do not have pistons which wind back as this is found commonly on older braking systems.
- To help push the piston back to position you can utilise a 'piston wind back tool', it is advisable to purchase or borrow such a tool as it often makes the task far easier.
- When winding back the pistons, you should not go past the inner face of the caliper, there is a risk if you wind the piston in too far you can damage the piston seal. If in doubt, please seek advice from a qualified mechanic.
5) You can now follow the removal steps in reverse by which to fit the new brake rotors and brake pads. At this point you should ensure that you have all required torque setting for the bolts you will be reinstalling, specifically: caliper mounting bolts and wheel bolts (or nuts).