

A COPY IS NOTHING MORE THAN AN IMPOSTER.
CHOOSE GENUINE OEM
REPLACEMENT BRAKES.
SHW PERFORMANCE, THE ONLY CHOICE FOR DIRECT REPLACEMENT GENUINE ORIGINAL BRAKE DISC ROTORS


ORIGINAL
EQUIPMENT.
ACCEPT NO
COMPROMISE.
Welcome to SHW PERFORMANCE, one of the world's leading brake disc manufacturers supplying directly to OEM, with product featured as standard equipment on many of today's new performance vehicles.
​
For the first time ever, SHW are now proud to offer the identical products, expertise and service directly to the consumer, granting access to true OEM replacement parts.
​
Learn more about the SHW range of products and discover how their innovation, testing and manufacturing techniques enable them
to remain at the forefront of brake disc
manufacturing.
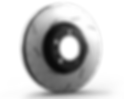



ONE OF THE WORLDS LONGEST ESTABLISHED BRAKE DISC MANUFACTURERS



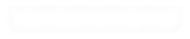



SHW PERFORMANCE produces both one and two piece, ventilated disc brake rotors to cover a wide range of vehicle applications.
​
The vehicle application automatically dictates which style, composition and type of disc brake rotor is available, as SHW only offer a genuine direct replacement for the factory supplied disc.
​
For lesser performance orientated vehicles, a ventilated monoblock disc brake rotor produced from cast iron will more than suffice. For vehicles placing greater demand on the needed stopping power, a lightweight, composite, fully floating two-piece design is often preferred (the style of which is referred commonly as a peg or pin drive system).
​
Rotor styles may also differ depending on application. From face drilling, alternative grooves to improve initial bite and pad cutting, or indeed a 'wavy' outer milled profile as shown.
​
THE ONLY TRUE
REPLACEMENT.
NOTHING LESS THAN A TRUE FACTORY EQUIVALENT





PIN-DRIVE BRAKE DISC ROTOR
PIN-DRIVE BRAKE DISC ROTOR
PIN-DRIVE BRAKE DISC ROTOR
Lightweight | Pin-Drive | Wavy | Cross-Drilled
Lightweight | Pin-Drive | Cross-Drilled
Lightweight | Pin-Drive | Drilled Bell



CAST IRON MONOBLOCK
PIN-DRIVE BRAKE DISC ROTOR
CAST IRON MONOBLOCK
One-Piece | Cross-Drilled
Lightweight | Pin-Drive | Slotted Face
One Piece | Plain Rotor Face

PERFORMANCE
UNDER PRESSURE.
Quality is a key ingredient from which to guarantee long term repeated reliability. SHW products are built to carry the high expectations required by exacting OEM standards and exceed them where possible.
​
Raw materials, advanced manufacturing techniques, high finishing standards, strict quality control procedures and rigorous testing are just some of the important foundations required to produce world leading brake rotors.
A further key element (and a notable advantage which SHW carry over the competition) is the advantage to encompass every step of production under one roof. With our own R&D facility to metal foundry and automated machining centres, SHW is truly responsible for every step of production from concept through to install.
​
Manufactured to perform under a wide range of conditions, from extreme heat cycles to withstanding corrosion in the harshest of environments, an SHW rotor performs well under all pressures.
​
​
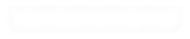


CONSISTENT RELIABILITY AND PERFORMANCE UNDER THE MOST DEMANDING OF CONDITIONS

Innovation, sustainability, added value. Welcome to SHW's patented Pin-Drive system, a substantial step forward in the future of braking.
​
SHW's Pin-Drive system carries many benefits when compared to conventional methods of disc brake rotor design. So, what is 'Pin-Drive' and why is it advantageous over a one-piece disc brake rotor?
​
The Pin-Drive system is a two piece fully floating disc brake rotor. The friction ring is connected to the central aluminium rotor bell by means of stainless steel pins which are cast into the assembly during the manufacturing process. The purpose behind the design is to offer a range of advantages:
​
- Up to 5.5lbs of weight reduction (rotating and unsprung weight) per disc compared to Monoblock.
- Reduced thermal strain thanks to the friction ring having more freedom to expand and contract.
- Low brake fading properties.
- Improved durability.
- Enhanced brake comfort thanks to optimised thermal conditions.
- Optimal curved vane design that maintains structural strength while improving noise dampening.
​
PATENTED DESIGN
PIN-DRIVE SYSTEM.
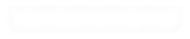







As well as a reduction in unsprung weight and improved braking characteristics, SHW's Pin-Drive design also prides itself on offering unbeatable cooling advantages, just one of the reasons why it has become the first choice for many OEM's.
​
Unlike other brake manufacturers, SHW developed a PATENTED improvement of the disc construction by offsetting the pin connection of the friction ring to the aluminium disc bell away from the center to the edge,
which results in huge cooling gains.
By offsetting the pin connection of the friction ring to the aluminium bell the cooling channels running centrally through the rotor see a huge increase in accessibility and cooler air flow. This advantageous design offers up to a 50% cooling advantage gain when compared to traditional designs.
Allowing a greater flow of air, heat generated on the surface of the friction ring (via the brake pads clamping down under braking) is carried away faster and more efficiently, dramatically reducing inner core and surface temperatures across the complete disc brake rotor. In addition, due to the unique patented design, further weight savings are achieved thanks to a shallow aluminium disc bell.
UNPARALLELED
COOLING ADVANTAGES.
FROM WEIGHT REDUCTION TO IMPROVED COOLING, DISCOVER THE BENEFITS OF THE SHW PIN-DRIVE BRAKE ROTOR SYSTEM
MAINTAIN OPTIMUM BRAKING PERFORMANCE FOR LONGER WITH IMPROVED COOLING PROPERTIES
The below diagram highlights the path of cold air entering the rear of the brake disc rotor assembly. The cold air is traditionally fed via air ducts located either in the front bumper, or channeled through pathways on the underside of the vehicles under tray.
As the cold air enters the rear of the disc bell, it passes through vanes between the two brake rotor faces. The cooler air helps to reduce temperatures from the very core of the brake disc by collecting heat and carrying it outwards, away from the brake disc assembly and eventually venting back out into the passing air flow found circulating the inner wheel.



Stainless Steel Pins secure the cast iron brake disc rotor to the aluminium mounting bell.
An Aluminium Brake Rotor Mounting Bell
(or 'Hat') helps to reduce overall weight
and rotational mass.



THE IMPORTANCE
OF AIR FLOW.
WHEN AIR FLOW IS PARAMOUNT TO PERFORMANCE. THE LOWER THE OPERATING
TEMPERATURES, THE HIGHER THE PERFORMANCE