

THE POWER OF IN HOUSE
MANUFACTURING
AN OEM APPROACH.
FROM INTIAL CONCEPT THROUGH TO PRODUCTION.
DISCOVER WHAT MAKES AN SHW ROTOR DIFFERENT
TO ANY OTHER

FULL CONTROL FROM WITHIN.
TO GUARANTEE REPEATABLE PERFECTION IS NO EASY FEAT
LEARN FROM SHW HOW IT'S DONE
Any brake related component is vital to the safety of any passenger vehicle, which is why investing into a quality product should be paramount when considering replacing factory components.
The only way to guarantee consistent and reliable quality is to take control of every aspect of manufacturing, something SHW takes very seriously. Discover more about the processes involved in the design, development, testing and manufacture of an SHW brake rotor, including:
- Conceptual design.
- Product design in CAD.
- CFD analysis.
- Thermal and structural mechanical simulation.
- Full model analysis.
- Casting process simulation.
- Development report and creation of associated drawings.
- Technical reviews and feasibility studies.
- Mold design.
- Mold production.
- Prototype manufacture.
- Product validation.
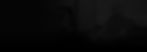
THE DESIGN
PROCESS.
FROM INTIAL CONCEPT THROUGH TO PROTOTYPE

The start of any brake rotor project first begins with the conceptual design. At this early stage there are typically many factors to consider such as; what is the intended application, the conditions surrounding it's expected use, vehicle weight and performance, available rim clearances, mating brake caliper size and possible pad friction area.
With criteria firmly in place and all necessary factors taken into consideration, the next step is to design the brake rotor as a CAD model. CAD models are not only used to create the finished product (by means of casting moulds, milling and turning), but also allow SHW to perform a range of vital tests to analyze safety and performance. Test included are:
CFD Analysis (Computational Fluid Dynamics).
The ability to analyze fluid flow in accordance with the components physical properties. For example; temperature, pressure and velocity are key data points necessary to optimize the design of SHW disc brake rotors. The data generated from the software enables SHW to analyse and refine the design to offer optimum air flow, heat management and more.
Thermal & Structural Mechanical Simulation.
This process is in place to measure and quantify the strength of the component or assembly. It typically highlights weak points in the design and displays where and when any structural failure could potentially occur.
Model Analysis.
This method of analysis looks at the overall components, investigating the general design, performance, strength and suitability for manufacture.

CASTING - THE SHW DIFFERENCE.
IN-HOUSE CASTING UTILIZING ONLY THE HIGHEST GRADE BLENDS OF CARBON ALLOYS

SHW is proudly the only brake disc manufacturer to encompass every step of manufacturing fully in-house. This allows maximum control over quality and ensures they are not reliant on third parties, thus always maintaining a reliable, repeatable supply of products globally. As well as machining and finishing centres, SHW also boast their very own Aluminium and Iron casting plants.
Each process, from casting to machining is fully OEM certified and controlled to the expected standards of OEM manufacture.
What makes a casting from SHW better than others?
Raw material (or indeed the casting) serves as the foundations for the finished product. Any imperfections or quality issues in the raw material would render the finished product substandard and potentially result in quality issues. Surprisingly this is a common occurrence with some brake disc manufacturers scattered across the globe.
SHW chooses to utilise only foundry iron for their casting requirements. In layman terms, this means that the raw material isn't recycled from scrap where it could be contaminated or below the required standards. Whilst this is a more expensive option, the fact remains that brakes are safety critical and not a component where financial savings should take precedence over safety.
In addition, SHW chose to opt for a proprietary blend of high carbon alloys to minimise distortion and eliminate thermal cracking under extreme temperatures, just one of the many reasons why a SHW brake rotor is more than just a replacement disc.

MACHINING &
SURFACE TREATMENTS.
INVESTMENT INTO AUTOMATION IN A STRIVE FOR PERFECTION

SHW have invested heavily over the years to refine and perfect the manufacturing process, especially the machining process.
SHW utilises a unique double disc milling process that is superior to any other way of standard milling. SHW turn mill’s the full brake rotor face over the entire surface at once (as oppose to standard milling). The result of this unique process provides a significantly more accurate and level surface finish, eliminates waviness, has zero runout and provides exceptional DTV (Disc Thickness Variation). Besides the tighter manufacturing tolerances achieved, this process also results in quicker bed-in procedures straight out of the box and reduces NVH (Noise, Vibration and Harshness) comfort issues.
During each process of machining, many key stages are
monitored for quality control:
- Monitoring of process parameters.
- Control of residual imbalance.
- Control of dimensions and tolerances.
- Control of resonance frequency.
- Visual inspection prior to surface treatment.
Once all surface machining is complete, the brake rotors then move on to the final finishing and quality control process.




SURFACE TREATMENT & QUALITY CONTROL.
THE CLOSING CHAPTER PRIOR TO DESPATCH
The final piece of this extensive jigsaw puzzle comes to completion with the surface treatment procedure. Each brake rotor needs to have a special coating applied to the surface, predominantly to provide a high level of corrosion resistance.
During this final stage the process is continually monitored to ensure:
- Testing of resistance to corrosion.
- Testing of adhesion to the surface.
- Control of coating thickness.
- Visual inspection of the final product prior to dispatch.
This level of detail ensures each brake rotor meets or exceeds SHW's internal Quality Control expectations, guaranteeing customers receive nothing short of perfection on delivery.